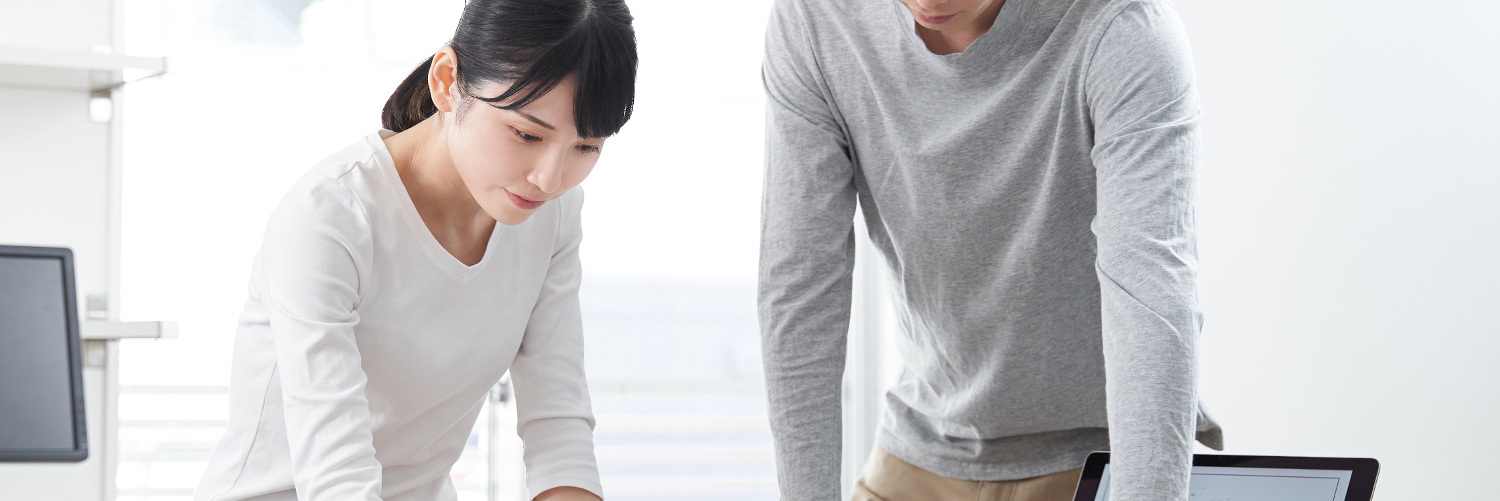
製品設計・開発
お客様の企画構想をお伺いしてから
量産に至るまでの各行程をご紹介します
製品設計フローのご紹介
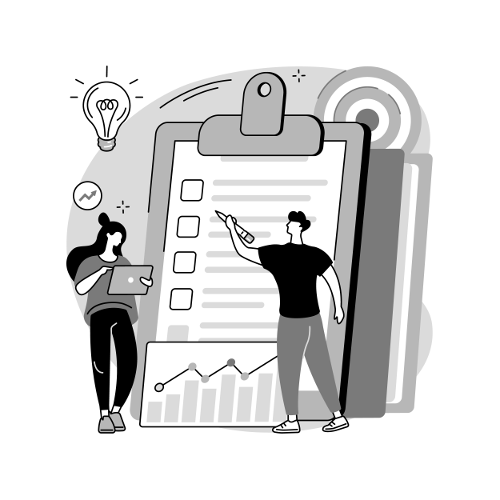
1.企画構想
お客様と詳細な打ち合わせからスタート致します。
何を作りたいのか、どうやったら上手くいくのか、どうやって評価していくのか※等、
製作目的、評価方法、使用期間、誰がどんなふうに使う等をお聞きし、形にしていきます。
※評価方法が確立しているか否かで、開発期間、市場での信頼性が大きく変動します。
2.設計構想
お客様の要望に、より的確に応える為に、設計・デザイン・製造、試作のプロ集団が検討を重ねて、仕様書を作り込みます。
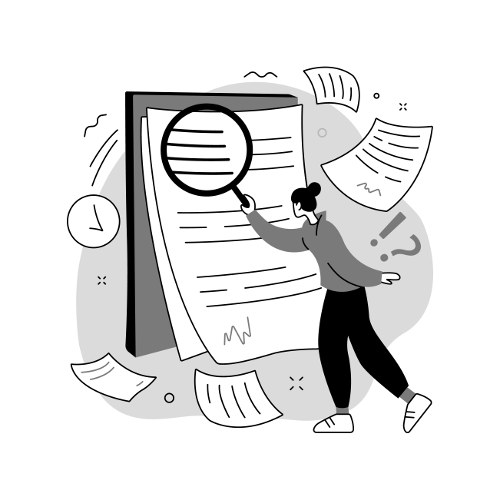
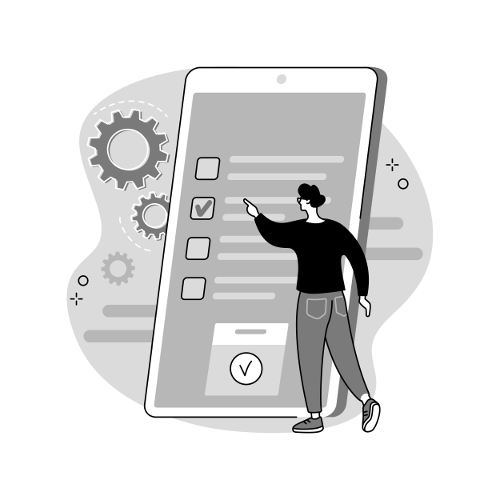
3.原理試作
機能や性能を限定しつつ実際に製品を作ります。
原理試作自体は、外観を確認するだけの動作しない試作品(モック)を作る場合もあります。
できあがった試作品で機能を達成できるか、市場ニーズはあるか(訴求力)を確認します。
また、評価結果を踏まえて、どこを改善すべきかを検討し、試作フェーズを進めます。
4.機能試作
製品が仕様通りに動くかを検証する試作です。
検証内容を決めて、機能試作1~3と段階を踏んで試作を行います。
【機能試作1】
実際の使用性、生産時のコスト試算、理想の性能がでるか、デザイン性はどうかを検証します。
【機能試作2/3】
機能試作1で出た課題への対策と実証をします。
金型成形する前段階の為、実際に使用する部品として問題ないかの最終判断をするタイミングになります。
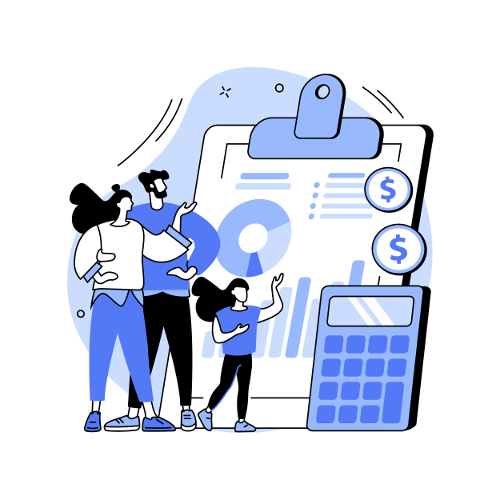
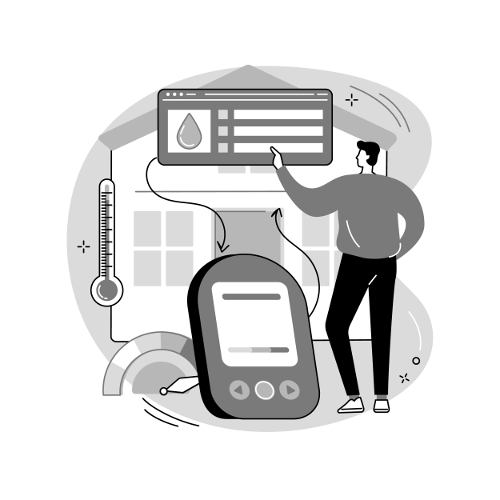
5.金型試作
各設計に問題がないかを検証するための試作で、量産用金型を製作し、以下の内容を確認します。
①信頼性評価試験
②許認可の事前試験の実施
③量産品として使う部材リストの確定
④量産工場・量産部品の品質確認
⑤量産方法(手順)を確定させる
6.量産試作
50台~100台程度を量産と全く同じ部材/生産ラインを使い量産します。
大量量産に移行しても問題ないかを検証します。
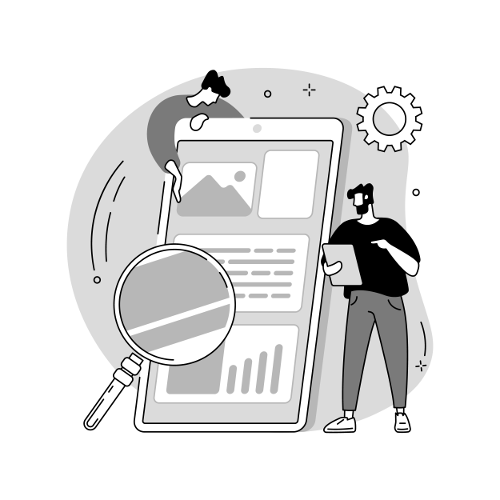
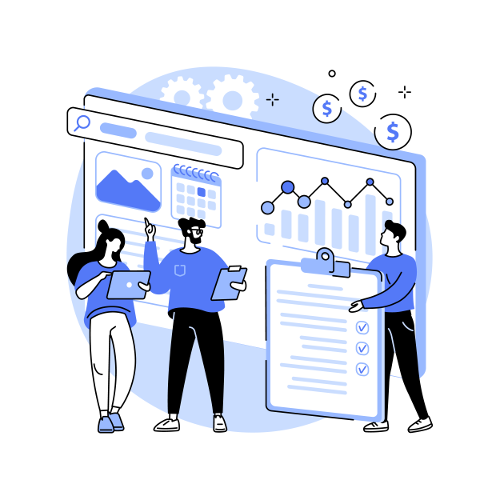
7.初期流動確認
(ローンチ)
量産が始まってからの初期段階の生産品に関しては、ロットバラつきやロット数量の影響を考慮して品質不具合を検出できるように高い検出感度で取り組みます。